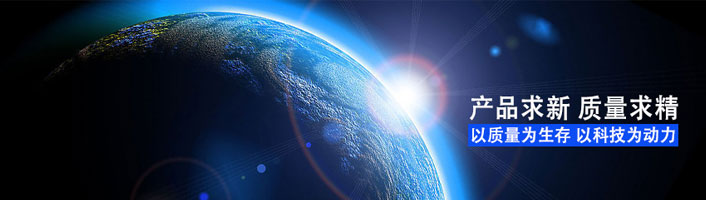
TPM点检管理与传统设备检查有哪些不同
TPM全员参加的生产维修,以“点检为核心”全员参加的生产维修,在设备上设立了区域管理的点检员,形成了点检管理制度。设备点检,完全改变了以前设备检查的业务结构,改变了设备传统性检查的业务层次和业务流程,创造了基础管理的新形式。TPM点检管理与传统的设备检查有哪些不同呢?具体来讲,有以下四个方面。
1、体现了设备管理思想的更新
现代化的技术装备,担负着社会大生产的重要使命,生产的产量、质量和经济效益将完全借助于生产设备来实现。往往一个小小的故障,将会造成自动化设备的全线停产,其损失之大是不可估计的。因此,设备在生产中的地位和作用将越来越重要,企业管理的重心也将更多地向设备管理转移,传统的管理思想,已不能适应现代化管理的需要。而设备点检的推行,恰恰是传统管理思想的更新,摆脱了传统管理的被动性,实现了管理意识强的点检维修方法——针对性维修。
2、达到了以管为主,工人参加管理的目的
传统性管理结构,是以修为主的体制,其管理业务(包括设备大检查)由职能机构的技术管理人员来完成。在推行“点检管理”后,其管理业务则由专职点检人员来具体实施,把管理的意识推向设备本身,真正体现了工人参加设备管理的优越性。因为点检人员是设备的直接管理者,他们最了解自己所管辖设备的种种状态,也最有制订维修计划、维修费用预算管理的发言权,而且最能反映其实际管理意识。
3、实现了维修的最佳化目标
以最经济的费用完成全部设备的维修工作量,以最少的故障次数和故障停机时间保证设备的正常运转,这是实行设备点检管理的两大最佳化目标。通过点检管理,能够定量掌握零部件的剩余寿命,均衡维修负荷,采取早期防范设备劣化的措施,把故障苗子消灭在萌芽状态之中,延长机件使用寿命,达到最经济维修的目的。
4、形成标准化的设备基础管理作业方法
为了达到设备管理的规范化,规定了各点检组的点检业务的内容、点检作业实施的路线、点检实施时间分配、点检作业图表记录以及点检实绩分析等和整个点检管理的标准化、规范化的事项。
相关推荐:
上一篇:石油化工企业如何加强机械设备管理
-
设备状态监测管理系统
-
设备点检管理系统
-
安卓无线点检仪
-
安卓无线测振仪
-
传感单元