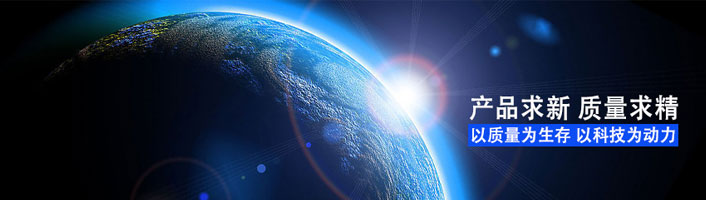
设备维修新理念--设备综合管理思想的提出
随着设备不断发展以及社会化大生产的出现,设备的故障对生产的影响越来越大,20世纪20年代美国首先提出了“预防维修”,自此,设备管理开始进入防止故障、减少损失的预防维修阶段。美国提出的预防维修,其基本含义是对影响设备正常运行的故障采取“预防为主”的措施,即在设备使用时加强维护保养,预防发生故障,以降低停工损失费用和维修费用。主要做法是以日常检查和定期检查为基础,从日常及定期检查中,了解设备实际状况,以设备状况为依据进行修理工作。
在20世纪30年代,前苏联也开始推行设备预防维修制度,这是以修理复杂系数和修理周期结构为基础的一种维修制度,按设备的复杂程度制订出各种修理定额作为编制预防性检修计划的依据,除了对设备进行定期检查和计划修理外,还强调设备的日常维护。
随着科学技术的发展以及系统理论的普遍应用,20世纪50年代美国通用电器公司提出了“生产维修”,强调要系统地管理设备,对关键设备采取重点维护,以提高企业的综合经济效益。
20世纪60年代,美国又提出了设备管理“后勤学”的观点。强调对设备的系统管理,设备在设计时必须考虑其可靠性、维修性。设备出厂后,要在图样资料、技术参数和检测手段、备件供应以及人员培训方面为用户提供良好的、周到的服务,以使用户达到设备寿命周期费用最经济的目标。从此,设备管理从传统的维修管理转为重视设计和制造的系统管理,设备管理进入了一个新的阶段——设备综合管理。
设备综合管理就是根据企业生产经营的宏观目标,通过采取一系列技术、经济、管理措施,对设备的制造(或选型、购置)、安装、调试、使用、维修、改造、更新直到报废的一生全过程进行管理,以保持设备良好状态并不断提高设备的技术素质,保证设备的有效使用和获得最佳的经济效益。
设备综合管理思想的两个典型理念是“设备综合工程学”和“全员生产维修制”。
1.设备综合工程学
设备综合工程学是由英国的丹尼斯,帕克斯于1971年提出的,并在英国工商部的支持下迅速发展和逐步完善起来的一门设备管理新学科,它以设备寿命周期费用最经济为设备管理目标,主要围绕四个方面进行:
1)对设备进行综合管理,即运用管理工程、运筹学、质量控制、价值工程等管理方法对设备进行技术、组织、财务等多方面的综合管理。
2)研究设备的可靠性与维修性。无论是新设备设计,还是老设备改造都必须重视设备的可靠性和维修性问题,以减少故障和维修作业时间,达到提高设备有效利用率的目的。
3)运用系统工程的观点关注设备的一生,包括设备从提出方案、设计、制造、安装、调试、使用、维修、改装、改造直至报废的全过程。
4)重视设计、使用、维修中技术经济信息反馈的管理。一方面是设备在使用过程中,由使用部门记录和积累设备在使用过程中发现的各种缺陷,反馈给维修部门,进行状态修理;另一方面,把设备使用记录和积累的设备在使用过程中发现的缺陷反馈到设备制造厂的设计部门,以便在研制新一代设备时加以改进。
2.全员生产维修制
全员生产维修制(TPM)是日本在设备综合工程学的基础上,结合日本的国情,提出的一套全员参加的生产维修方法。其特点是:
1)把设备的综合效率作为最高目标。
2)强调全体成员参与,即从企业总经理到每一个操作员工都参加设备管理。
3)建立以设备一生为对象的全系统管理体制,包括设备计划、使用、维修、财务等所有部门。把设备的日常点检、定期检查作为实行计划预防修理的依据。突出重点设备,把重点设备的计划预防维修同一般设备的事后修理结合起来。
相关推荐:
上一篇:设备故障诊断之振动诊断技术
下一篇:设备操作工的岗位点检的重要性
-
设备状态监测管理系统
-
设备点检管理系统
-
安卓无线点检仪
-
安卓无线测振仪
-
传感单元