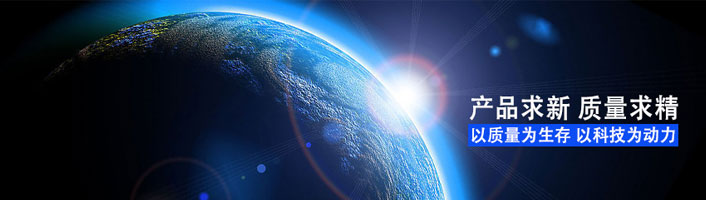
2019全球自动化和制造主题峰会-郭朝晖谈工业智能化
9月18日,备受业界瞩目的2019(第八届)全球自动化和制造主题峰会在上海盛大举行。本次会议邀请到了上海优也信息科技有限公司首席科学家、原宝钢研究院首席研究员郭朝晖博士出席并做主题报告。本文为郭朝晖博士的演讲实录,略有删减。
下午好!今天非常荣幸来跟大家分享一下我对智能化的看法。
五年前我还在宝钢的时候,给公司领导提了一个建议:关注一下智能化和工业4.0。至今大概有五年左右时间了,在这个过程当中,我想我的许多经历可能跟大家差不多,我们都听到了很多糊里糊涂的概念,似乎是明白了,也似乎是不明白。今天,就向大家汇报一下我的一点思想历程。
现在有一种不好的趋势:别人怎么做的,我要跟着怎么做。这样做往往是失败的。这种现象目前也非常多。
我在宝钢研究院工作了20年,担任了15年的首席研究员,期间一直都在想:创新到底是为了什么。作为一名企业人员,我们做的是要创造效益,怎样才能发挥效益?这就要把技术用在一个合适的地方。
我非常敬重宝钢老领导何麟生说过这样的一句话,“价值决定于用户,不是决定于技术本身”。半杯水丢在桌子上是垃圾,放在沙漠当中就能救命。同样,5G也好,人工智能、大数据的技术也好,关键是要把技术用对地方,要把技术用好,一定得知其然,知其所以然,而不是单纯的模仿。因为人家用的好东西,到你这不一定合适。我今天就是跟大家谈谈如何用好技术的问题。
我觉得,我们是在前瞻未来的时候,一定要回去看看历史。看看这个事情是怎么一步步走过来。
所以,今天我给大家的汇报分成三个部分:其实就是过去、现在和未来。我主要以宝钢作为例子来说,但不管是流程还是离散制造业,背景和道理都是相通的。
首先,我来介绍一位老先生,他叫何麟生,今年90岁。我曾经把他的几篇文章拿给一些知名专家和高层领导去看,他们很难相信这是何老在30年前就说的话。这些观点放到现在,仍然非常先进。
何老认为:认识信息化有很多角度。其中一个就是对知识的管理。他说他在宝钢时的职位可以被叫作CTO,也可以叫CIO,但是他更喜欢被叫作CKO,也就是首席知识官。大家听到这里,可能会有种似懂非懂的感觉。所以,要把何老先生讲话的背景讲一下:一个现代化的企业,是怎么管理的?
现代化企业的管理一定是建立在一整套的标准之上。否则,根本就谈不上是个现代化的企业。在宝钢,就有很多标准。其中一类标准就是以产品为线索的。首先是产品的标准,来定义用户的需求。第二是技术的标准,来定义每个工序是怎么做的。接着是如何做到,也就是作业标准和手顺书。
何老讲的知识,其实就是这些标准。这些标准在宝钢建立之初,就必须放在计算机里。道理很简单,以轧钢为例,几分钟一块钢就过去了,期间很多工艺参数需要下达。如果一个参数错了,就会出问题。对于这类问题,人可能忙不过来、也容易出错。所以这些知识必须要计算机去执行。当钢来了之后,计算机根据工艺要求把它下达出去。
我们注意到:相当多的标准,包括产品标准和技术标准,其实都是可以用一个数据结构来描述。一块钢坯来了之后,计算机读取数据结构,然后按照这个标准进行执行控制。
但是,仅有这样的标准是不够的。如说化工厂,生产状态发生变化了之后,固定的标准就不合适了。这时,往往涉及到一个动态调整标准的过程。同样,用软件来解决这些问题,能做得更好。
于是,我们又需要一种软件承载的知识。在钢铁行业叫做模型,在化工行业中叫APC(先进控制)或者RTO(实时优化)。
我们再看看工业的发展历史,在这个历史过程当中,我们也能从知识的角度来分析历史怎么发展。
工业1.0的阶段用机器操作,或者甚至再往前手工操作,那个时候许多知识是在人的脑袋当中的,你制造一个汽车,会有师傅交给你怎么来做。但是到了2.0之后,到了流水线之后,它有一个巨大的改变。这个改变就是把一个加工过程变成若干个岗位上简单化的操作。有的人专职拧螺丝,有的专门敲榔头。所以,一旦流水线化了之后,他就可以把工作过程解析开来,进行标准化。标准化了之后才容易让机器去做。换句话说,工业2.0时代已经把知识解析和标准化。
到了3.0时代,有了计算机了,我们就可以把这些放到计算机里。但3.0阶段处理,计算机处理的问题还不够复杂。因为很多复杂的问题是人来做的。如质量异常的处置。工业4.0阶段需要把大量知识放到计算机里,解决这些过去人去做的事情,于是有了智能化。
所以工业发展过程,可以从知识的角度去看。而现在的智能化过程,还有一个重要的趋势,就是通过互联网实现知识的共享,把获得知识的成本大大降低。从而促进了智能化。
下面我们再来谈谈当前所遇到的问题。我先给大家讲两个故事,来说明知识软件化是怎么回事。
刚才谈到,自动化阶段的知识多数可以用数据结构表述。但这些数据结构是怎么来的,我们却不知道。
大概在这个世纪初,宝钢在生产冷轧板的时候遇到一个问题:轧机的能力不够了。这个时候我们找到了国外的设备供应商,国外专家认为你们应该做改造。仅仅更换一个马达就要1.3个亿,而且要影响生产。要知道,当时的冷轧厂的生产就像印钞机一样,影响非常大。
宝钢的冷轧机是5个轧机一起工作的。需要一个负荷分配表来分配五个轧机的工作。这个表,就是我前面讲到的“数据结构类知识”。这时,宝钢有位老专家、我的前辈和同事朱泉封发现:按照国外给的表格,有的轧机已经接近100%的负荷、确实没有办法提高了。但是,有的轧机却负荷不高。但负荷高的这一台,限制了整个轧制机组的能力。这张表格过去是从国外引进的,但引进的时候没有考虑到要轧这样的板材。这是问题的根源。
朱泉封先生提出了另外一个思路:修改轧制负荷设定的表格。
但是,我们引进的就是这样的一个表格,人家没有告诉我们这个表格是怎么产生的。人家应该有计算表格的办法,但引进的时候不会告诉你。因为这是人家的核心技术。
于是,朱先生根据他对轧钢原理的理解,给出了计算模型。按照新计算的负荷分配轧钢,结果一次性成功。
另一个案例也类似。我们有次接到一个特殊要求的合同。连铸生产了6000吨,结果只有一半合格。损失几百万。后来我们发现,有几个参数有问题。这些参数同样是国外给的。我的同事过去一看,用我们自己的软件计算了一套新的参数。用这套参数试一下,结果出奇的好。
这两件事有一个共性,就是当企业在开发新产品、特殊产品时,就容易发现这样的需求。据说在美国的波音公司,这种类型的软件有5000多款。
但这技术都是人家核心的东西、不一定会对外宣传。我们很多企业引进了国外的生产技术,人家却不一定告诉你这些与研发、创新相关的技术。我们很多企业甚至根本不知道有这样东西。所以,如果企业没有达到一定的高度、很少有新产品研发,也就没有这样的需求、也就不理解工业知识软件化的意义。换句话说,这些技术的需求,往往是研发和设计推动的。
类似的道理,可以推广到中国的工业软件。我们知道,CAD、CAM软件几乎被国外垄断了。为什么呢?我看一个重要的原因在于我们的工业企业过去没有达到这样的程度,工业软件企业就缺乏市场。比如,我们值得骄傲的企业上汽大众,在二十年前几乎就只生产一款桑塔纳,别的都不生产。没有研发、没有新产品设计,要这些软件干什么用呢?相反,我国的航空企业在这个方面走在前面。一个重要的原因就是:航空有需求——军用飞机需要自主研发。
所以只有企业发展一定程度之后、开始重视研发了,才能意识到这个问题是重要的。中国现在整个工业企业都在转型升级,这个需求就提出来了。所以,很多企业觉得“工业技术(知识)软件化”是个突然冒出来的概念,也就不足为怪了。
我按照自己的理解,给工业互联网白皮书的副标题做了一个翻译:重构人和机器的界面。我们还写过一本书叫《三体智能革命》。这里面我们有一个观点,智能化很大程度就是把人脑当中的知识放到计算机里。这两个观点跟现在很多人的说法是不一样的。有人甚至认为,智能制造就是人工智能、深度学习在工业中的应用。我个人认为:依靠深度学习获得的知识,是工业知识中极少的部分。
除了图像识别,机器学习在工业中的应用场景有限。智能制造需要知识,深度学习获得的知识不是主食,只是佐料或味精。
智能制造所需的主要知识,应该是从专家的脑子里转过来的。所以我们可以看看,现在那些知识还依赖于人脑。在研发、设计、异常处置、用户服务等方面,大量的工作是由人类专家来做的。我们应该尽量把其中的一些知识变成标准化的东西。只有数字化、显性化的知识才容易传承。
刚才说的连铸的事,我当时从日本人学过一些东西。我发现了一个特点,日本人做任何一个事情,人家不是拍脑袋。人家做什么事情都给你写一个规范,你拿过来就按照这个规则就能做事。
我在研究日本人的东西时,发现它给的规则是有问题的。但是,这比没有规则强,为什么?因为出了毛病的时候,你可以研究毛病在哪里、可以去改进。你如果连规则都没有,你改什么呢?
在我看来,智能化的过程往往就是把人脑子中的一些知识拿出来。不要搞得很神秘,搞的神秘的人是因为他不懂。我再给大家举一个例子,这个例子是我在优也做首席科学家时提出的:我们搞智能化,就是把人的知识转变成计算机的知识。
优也是个咨询公司,专门帮助别人搞优化,尤其是搞节能。我们的咨询师到了现场,发现锅炉热效率低了三个百分点。这些损失就是潜在的效益。下一步,要找到根源。发现是烟道堵了、传热效率低了。接着就是找到办法:清扫一下。最后,把结果报告管理层,问题就解决了。
这是咨询师能做的事情,智能化能怎么做?就是把人的逻辑数字化、模型化:你凭什么知道效率低了三个百分点?你把你的逻辑告诉我,我把数据收集上来,我按照你的逻辑来算。你凭什么知道是烟道堵了?你把你的逻辑告诉我,我把数据采集上来,我按照你的逻辑去算。你再告诉我什么时候应该让他扫灰,我发的指令和他扫灰之间的间隔是多少?在年终的时候,领导可以根据这个东西来论功行赏。智能化千万不要想复杂了。
美国的大河公司其实就是按照这个逻辑走的。按照这个逻辑,我们管一个质量组有几十人上百个人,据说人家只有几个人。这是现在。
但是,“把人脑中的知识放在计算机里”其实也不那么简单。因为这些知识是碎片化的、不容易管理;因为把这些知识放入计算机的时候,可能会影响正常生产。这是一个曾经困扰我很长时间的一个问题。
我们再来看看为什么出现工业互联网平台和工业APP?
自当工业互联网出现了之后,你就会发现我们需要知识数字化的地方很多:因为很多管理问题可以用数字化模型化方法解决了。
许多人困惑于工业互联网的机会在什么地方。对此,我有个观点:过去能做的事情,就不是现在的机会。我们研究一些企业的控制和信息系统就会发现:过去的系统存在一个问题:响应速度快和管控范围大是不可得兼的。比如,基础自动化响应速度快,控制的范围却小;企业的ERP管理的范围大、实时性却差。而工业互联网能让我们突破这一悖论。所以,工业互联网带来的机会,往往在于全局优化、尤其是全局实时优化。
我所服务的优也公司的一项实践,就说明了这个道理。钢铁企业的煤气,是个需要实时管理的资源。但这个资源的生产和使用范围,涉及到几个平方公里、乃至几十平方公里的范围。过去主要靠人来管理,就管不好。利用工业互联网这样的手段,就有条件管好。在华东地区的一个不大的钢厂,通过工业互联网技术的应用,每年创造了4200万效益。
谈到全局优化,麻烦事又来了:怎么才能搞好顶层设计呢?这个问题困惑了我很久。后来意识到:一次性地把顶层设计搞好往往是不可能的。应该采取持续改进的方式来解决问题。
日本的IVRA架构非常值得研究。这个架构有三个维度。一个维度是从管理开始,争取把质量做的最好,成本降到最低,交货期搞的最短,环境搞得最好。企业能做到这样就一定很牛了。管理针对什么呢?针对资源。如人、产品、过程等。怎么搞呢?PDCA的手段——也就是持续改进,走从量变到质变的路子。
对工业人来说,这个架构里面没有什么新东西,都是过去强调过的。但是,你现在的PDCA是在计算机里进行的。PDCA在计算机里面进行的话,你的管理能力将会大大地增长,超出过去的水平:任何问题都管得细、管得及时、管得准确。
按照这个思路,需要把一些管理和技术的知识沉淀下来。但这时,又会带来新的麻烦:需要沉淀的知识是碎片化的、知识沉淀和修订是日常化的。传统额信息系统难以承担这样的任务。于是,工业互联网平台技术应运而生了。
工业互联网本质作用,是让知识持续沉淀的过程风险降低,质量提高,成本降低,速度加快。我曾经打过一个比方:在过去的软件系统中增加一个功能,就像建栋大楼非常麻烦;现在增加一个功能就像搭个帐篷,非常简单。这个帐篷,就是沉淀的知识,就叫做工业APP。
比如,过去增加一个功能的时候,需要从很多设备上取数据。不仅麻烦,而且会对生产带来风险。现在,我们把一些准备工作实现做好,需要数据的时候直接从平台上拿。这样,工作量和风险就降低了。
有些工业互联网平台(如ThingsWise平台)采用了数字孪生技术。这种技术的特点,是实现了知识的复用、有利于专业分工协作。这又进一步降低了风险和成本。
我们设想一下:假如一个APP能够带来100万的效益,而开发成本却要150万。这样的APP就不具备经济性。反之,如果开发一个只需要10万元,则会具备经济性。所以,工业互联网平台降低了知识沉淀成本,也就让智能化的持续改进之路容易走了。
这就是我今天跟大家的汇报内容。最后,我强烈地呼吁大家不要跟风。做任何一个东西要知其然,又要知其所以然。知道为什么要做,才能做到“不忘初心”,才不容易做错。
-
设备状态监测管理系统
-
设备点检管理系统
-
安卓无线点检仪
-
安卓无线测振仪
-
传感单元