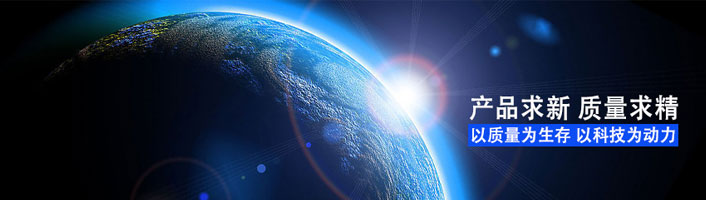
改善精益体系需要的五个步骤
精益专家沃麦克和琼斯在出版《改变世界的机器》一书后,之后又用4年的时间,经由访谈、深入研究,于1996年出版了《精益思想》一书,于2003年修订再版,淬炼、总结了精益实践的五个步骤。下面看看在持续改善的精益体系中,企业如何发现自身的改善之路吧。
一、定义/识别价值
精益实践的关键出发点是价值,而价值只能由客户来确定。而提供错误的产品或服务是一种“浪费”。
请注意,“精益”不是制造系统的目标,“价值”才是制造系统的目标,客户的价值认知和我们的成本与努力无关。
我们要以客户价值认知作为精益的起点,形成决定性竞争优势,作为发展制造系统的目标。如果“目标”错误,后续发展的制造系统会是一项“浪费”。
很多情况,竞争对手未察觉产业或运营模式问题,而检视业界造成客户的问题,是识别决定性竞争优势的起点。
二、识别价值流
特定产品的价值流包含三项关键管理任务,这三项任务是:
①从概念,产品企划、设计,到投产全过程的解决问题任务。
②从接单、制定生产计划再到交货全过程的讯息管理任务。
③从原材料到成品,送到用户手中的物质转化任务。
价值流分析能显示出沿价值流的三种活动:
能创造价值的步骤,如机加工改变物理形状的过程。
虽然不创造价值,但是在现有技术与生产条件下不可避免的步骤,如为保证品质,焊接处要检验(称为1型浪费) 。
不创造价值而且可以立即去掉的步骤(称为2 型浪费),如去毛刺 。
三、流动
一旦精确定立了价值,也完整地制定出了某一特定产品的价值流图,消灭了明显的浪费步骤,实行精益思想第3 步的时机也就到了,让保留下来、创造价值的各个步骤流动起来。
为因应波动的冲击,应善用缓冲,例如:时间、产能或库存缓冲,平衡流量吸收波动的冲击,以免在拉动时一拉就断。
四、拉动
"拉动"一词最简单的意思是, 在下游客户提出要求之前, 没有一家上游工序或企业生产产品或提供服务。
使用拉式系统的好处:
降低成本:在制品数量低且返工更少。
提高品质:存在追求内部品质和更好的检测能力的压力。
更好的客户服务:提前期短且产出可预测。
更大的灵活性:只有当系统状态容许加工工件时,工件才会被拉入系统。
《供应链科学》[1]给出推式系统与拉式系统定义:“如果一个系统内的工件根据系统的状态投料,并且因此给在制品水平加上一个内在的限制,那么这个系就是拉式系统。如果一个系统内的工件不管系统状态如何就进行投料,并且因此没有内在的在制品数目限制,那么这个系统是推式系统”。并指出“拉式系统的魔法在于限制了在制品数的最大值。”
界定推式与拉式系统的两个关键词:“系统状态”与“限制在制品”。根据定义,即使依库存耗用或瓶颈产能负荷投放工单,没有限制在制品数量的面向库存制造是推式系统,而不是拉式系统。
五、尽善尽美
持续进行根本性的、不断的改善,需要学习和观察价值流、价值的流动、被客户拉动的价值,使得尽善尽美变为清晰可见的图像,因而使人们能看到改善目标,并且使这个目标对于整个企业都是现实的。集中精力消灭浪费、减小波动、缩短提前期,以需求出发,解决问题,不要让惰性成为系统进步的制约。
在尽善尽美的改善过程中,会面临“鼓励改善与裁减员工”的冲突,员工卖力改善了,却因为效率提高被裁减了,这样的话,员工就不会安心地投入到改善中来。适度增加竞争性是应该的,但是更多地是需要给员工定心丸,树立负责任的企业形象,并共同分享改善带来的成果。
我们要如何以精益五步骤落地精益生产呢?彻底杜绝浪费,以最小缓冲成本,根据系统状态投料,限制在制品数量,由客户拉动价值,畅流价值流,交付价值。希望以上五步骤对您有所启发。管理者应正确地识别、定义价值,建立自身的决定性竞争优势,打破市场瓶颈,赚更多的钱,让基业长青。
-
设备状态监测管理系统
-
设备点检管理系统
-
安卓无线点检仪
-
安卓无线测振仪
-
传感单元